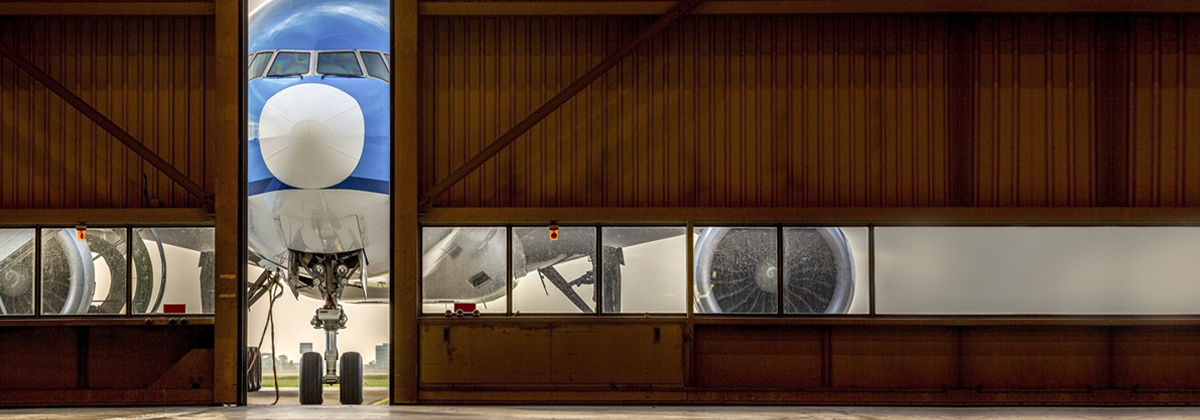
Whether you are in the business of repairing your company’s aircraft or providing airplane overhaul & repair services to customers, you are already aware of the astronomical expenses that are involved with such projects. But it would be best if you also were mindful of the cost-saving options available to you when it comes to repairing avionics or airframe parts. In this article, we will break down various ways you can significantly reduce time and cost when repairing your aircraft.
PMA Certified Parts
PMA (Parts Manufacturer Approval) parts are aircraft parts that have received both design and production approval issued by the FAA, even though the OEM didn’t manufacture them. So they are, basically,
The existence of PMA offers competitive pricing on airframe parts that can amount to hundreds of thousands of dollars in savings. You can either search for PMA aircraft parts online by registering to ePlane for free, or do the legwork and contact distributors and repair stations in your vicinity and make sure they carry PMA parts in stock.
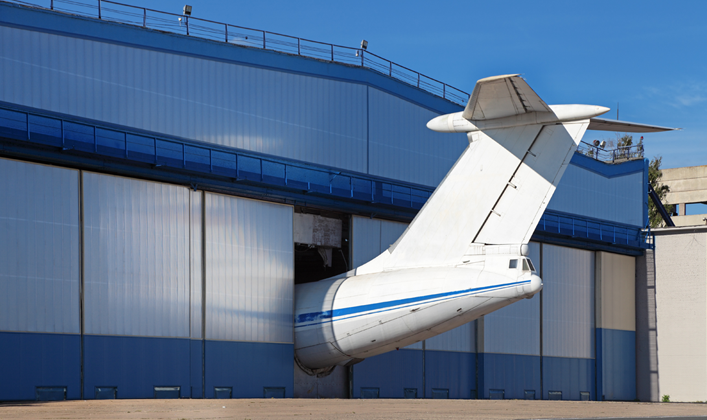
The existence of PMA offers competitive pricing on airframe parts that can amount to hundreds of thousands of dollars in savings.
Spare Parts
Most flight departments, charter operators, and air-evac aircraft that fly over 400 hours per year, typically carry an inventory of spare parts, components & equipment for high-fail PNs on hand. This way, you can avoid extra downtime and over-priced AOG services. Just consider the cost of re-booking or postponing a flight. It makes more sense to keep high-fail items on hand (EFIS displays, weather radars, etc.).
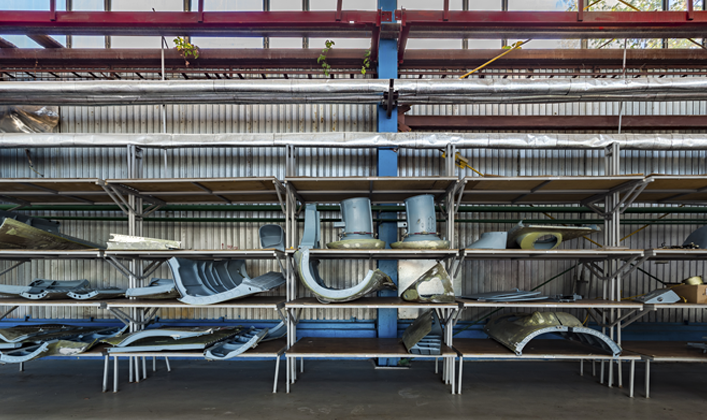
Most flight departments, charter operators, and air-evac aircraft typically carry an inventory of spare aircraft parts.
Aftermarket Parts
When it comes to ‘As Removed’ parts, most people wrongly believe that an 8130 grants you a license to install an aircraft part and that without it, the part is null. This belief is inaccurate because the absence of an 8130 does not disqualify a component from returning to service, even though the lack of tractability CAN be a major issue.
MROs that deal in aftermarket avionics parts remove equipment daily, as part of upgrading aircraft and installing brand new technology. Most of the parts are removed from operational aircraft, a fact that allows for full traceability. Certified suppliers will give you full traceability and part’s CoC (Certificate of Conformity) with every part or component you purchase. In addition to assuring that the parts are fully serviceable, this practice also saves you standard repair processes and OEM bench tests that will not necessarily enhance the functionality of your unit. This alone can save you up to half of the cost of exchange or repair.
ADS-B Out Specifications
By December 31, 2019, any airplane that operates in controlled 10,000-feet airspace in the US, will need to be ADS-B Out (Automatic dependent surveillance-broadcast) compliant. Aircraft that are equipped with ADS-B Out continually transmit airspeed, altitude, and location data to ADS-B ground stations. These regulation guidelines call for the installment of particular transmitters (1090 MHz Mode S transponder or 978 MHz UAT) in over 100,000 airplanes, an upgrade that can be extremely expensive. However, there are low-cost options that can work within a given avionics suite by swapping transponders. These solutions also include valuable ADS-B IN possibilities as well
Other cost-effective solutions are STC (Supplementary Type Certificate) packages for several different airframe and avionics suite combinations. Some come with installation kits that consist of all parts and instructions that are needed for the upgrade.
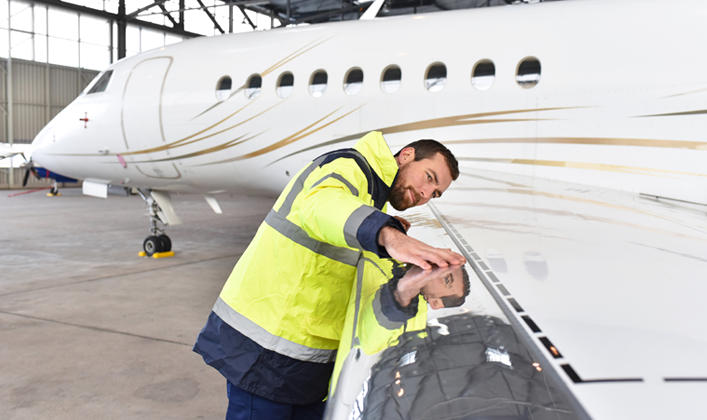
Aircraft that are equipped with ADS-B Out continually transmit airspeed, altitude, and location data to ADS-B ground stations.
Recycled aftermarket Airframe Parts
Although very difficult to find, there are several ways you can procure fully serviceable recycled aftermarket airframe parts. In today’s aerospace market, there are a couple of organizations that promote the decommissioning and recycling of aircraft parts. One example of such an organization is The Aircraft Fleet Recycling Association (AFRA), an international non-profit association that advocates environmental and sustainability practices in the field of aircraft disassembly and repair.
Recent research indicates that the commercial aircraft disassembly and recycling market will experience significant revenue growth rates during the next decade, as airlines worldwide switch to new generation fleets in their quest to reduce maintenance costs, improve operational efficiency, and minimize noise & air pollution. The retired aircraft are being decommissioned and disassembled, flooding the aftermarket with fully functional, cost-effective, salvaged parts & components.
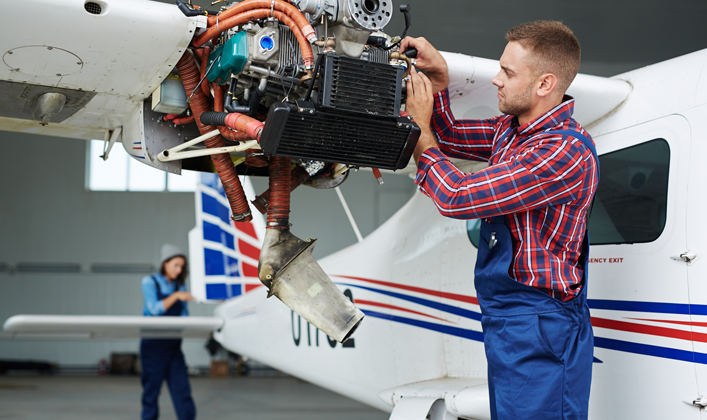
There are several ways you can procure fully serviceable recycled aftermarket airframe parts.
When Should You Upgrade Your Avionics Suite?
New certified avionics suites offer the advantage of new features and capabilities. You may not necessarily need these tweaks, but as the market begins to understand the benefits, the suites rise in popularity, and the available slots in the shops gradually dwindle. Waiting to upgrade may not be the smartest strategy, and it can even have grounding consequences. Upgrading is almost always inevitable, but the timing is the most crucial factor. While keeping the aircraft in the air is your number one priority, the urgency of any upgrades is open for debate. You can either wait or be first in line to get it done; experience and business analysis should be your two primary deciding factors.
Understand All Your Options
The best path to substantial cost savings for you and your customer is recognizing all the different options available before making any decision. ALL aircraft parts eventually break; with focused research and aftermarket knowledge, you will be able to make a more informed decision for your customer or your own business. This approach reduces aircraft AOG problems, and it also boosts your reputation with customers & partners while establishing you as a problem-solver and authority in aftermarket issues.