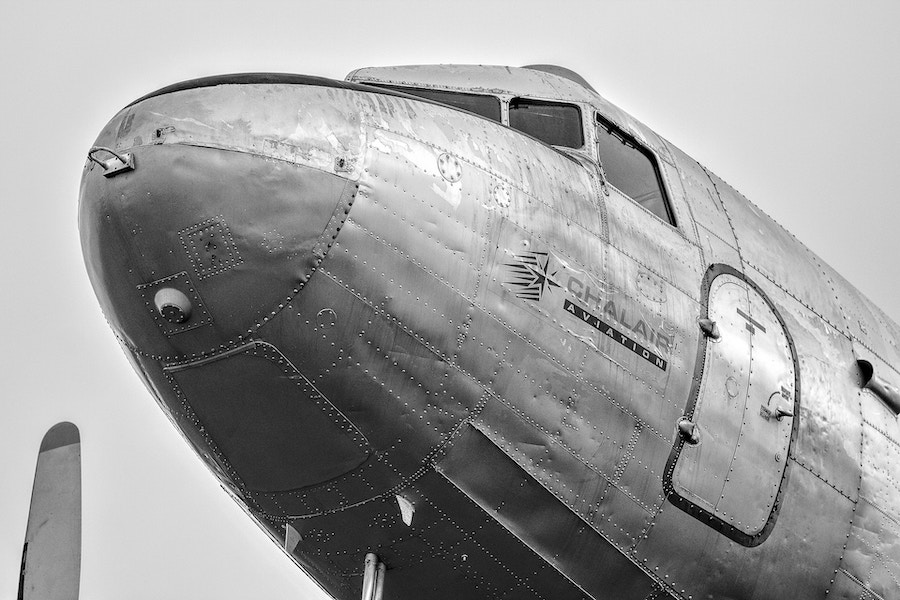
Corrosion, a natural process where metals deteriorate due to environmental interactions, poses significant challenges in the aviation industry. Airplanes, primarily constructed of metals like aluminum and magnesium alloys, are especially vulnerable to corrosion.
This degradation can absolutely compromise the structural integrity of the aircraft, leading to potential safety hazards and increased maintenance costs. Therefore, understanding the types and effects of corrosion is paramount for ensuring the longevity and safety of aircraft.
Aircraft corrosion manifests in multiple forms, each with its unique characteristics and implications, ranging from the aesthetic roughening seen in surface corrosion to the more insidious effects of filiform or pitting corrosion. Not all types pose the same level of danger or require the same resource-heavy solutions.
Filiform Corrosion
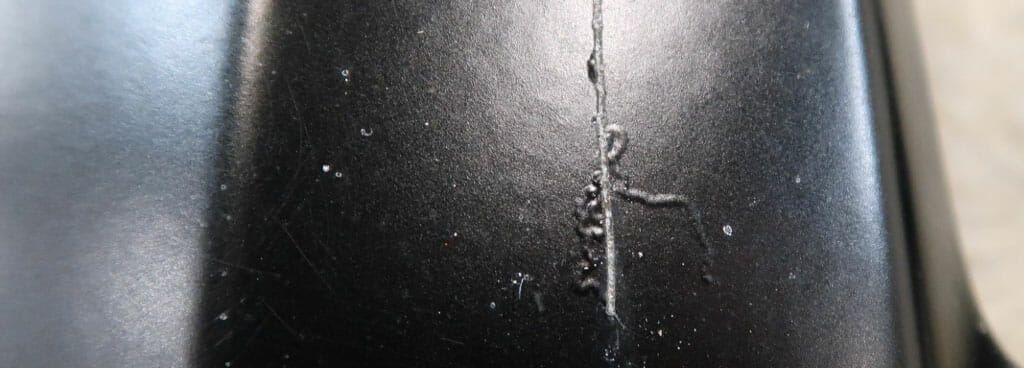
Filiform corrosion is a unique type that manifests as thin filaments or threads beneath a metal’s coating, such as paint or other protective layers. These filaments spread out, often in a random web-like pattern, causing the coating to lift or bulge. The corrosion typically starts at a defect or breach in the coating, allowing moisture and other corrosive agents to penetrate and initiate the filiform process. With time, the filiform corrosive damage will worsen. However, it’s not nearly the most detrimental type of corrosion an aircraft can face, as it jeopardizes the appearance more than the mechanical capabilities of the plane.
Filiform corrosion is particularly problematic for an older aircraft due to recent advancements in combating this type of corrosion through evolved outer coats.
Filiform Corrosion’s Appearance on an Aircraft
This type of aircraft corrosion is earmarked by its distinct pattern of undulating lines beneath the coating, resembling trails left by worms or the fine roots of creeping plants. These filaments can cause the coating to lift or bulge.
Filiform Corrosion’s Impact on Aircraft Metals
- Coating Integrity: The corrosion can compromise the protective coatings, exposing the metal underneath to further corrosion.
- Aesthetic Concerns: While it might not always compromise structural integrity immediately, it can lead to unsightly patterns on the aircraft’s surface.
- Potential Structural Concerns: If left unchecked, the corrosion can spread and weaken the metal beneath the coating.
Filiform Corrosion’s Prevention and Treatment
- Proper Coating Application: Ensuring coatings are applied correctly, without defects or breaches.
- Environmental Control: Reducing exposure to high humidity and acidic conditions.
- Regular Inspections: To detect early signs and address any breaches promptly.
Pitting Corrosion
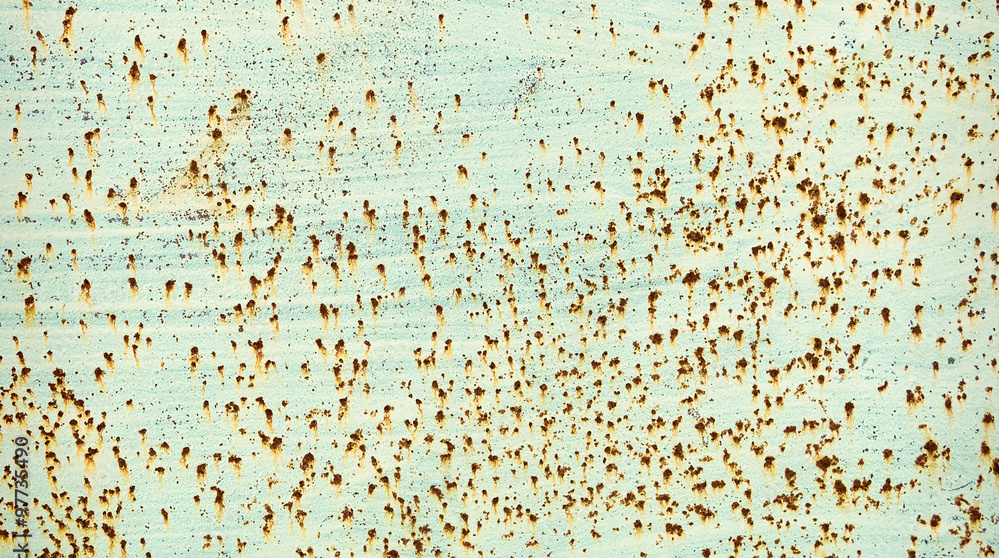
Pitting corrosion is a localized type or form of aircraft corrosion, resulting in small cavities or “pits” on the metal surface. The most common culprit? Trapped moisture, making tight crevices particularly vulnerable. This type of corrosion targets specific areas and can penetrate deep into the metal, making it much more serious than the above-mentioned filiform corrosion. If not addressed or removed, it can lead to unsafe stress-corrosion cracking (further explored later in the article).
Important to note is that pitting corrosion can strike a wide variety of alloys, but is most associated with aluminum and magnesium.
Pitting Corrosion’s Appearance on an Aircraft
The pits can be shallow or deep. Due to their often microscopic size, they may be challenging to detect in the early stages, especially as they may be concealed under a dust-like substance. The surface might display a tiny pit, but extensive corrosion could be occurring underneath.
Pitting Corrosion’s Impact on Aircraft Metals
- Structural Weakness: The pits can serve as initiation sites for cracks, potentially leading to catastrophic failures.
- Hidden Dangers: The depth of these pits can be deceptive, with extensive corrosion weakening the structure beneath a seemingly minor surface blemish.
- Material Loss: Even if the overall material loss is minimal, the structural integrity can be significantly compromised.
Pitting Corrosion’s Prevention and Treatment
- Regular Inspections: Using advanced techniques like ultrasonic testing to detect even microscopic pits.
- Protective Coatings: Application of corrosion-resistant coatings to vulnerable areas.
- Material Selection: Using alloys less susceptible to pitting.
Surface Corrosion
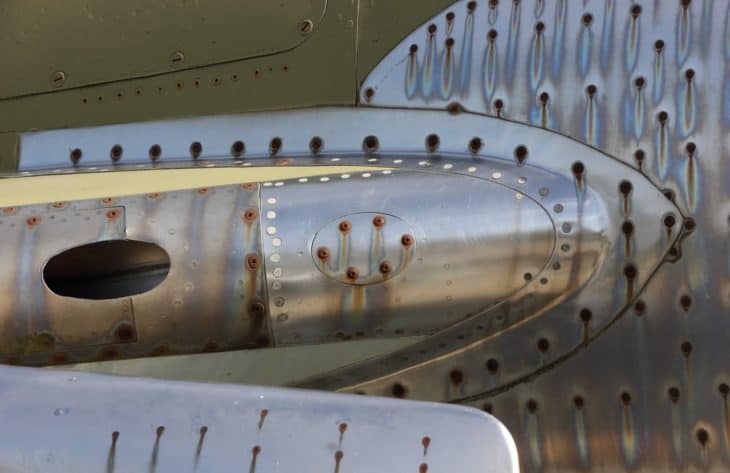
Surface corrosion, also known as uniform corrosion, is a widespread form of metal degradation that affects the entire exposed surface at a relatively consistent rate. It arises from the metal’s direct interaction with environmental agents, leading to a uniform loss of material from the surface.
While it might not penetrate as deeply or as rapidly as some other aircraft corrosion types, its cumulative effect can significantly weaken the metal over time, posing potential risks to the aircraft’s structural integrity.
Surface Corrosion’s Appearance on an Aircraft
The metal begins to display a roughened texture, which can advance to pitting or etching in severe stages. A notable sign of surface corrosion is the emergence of a gray-white chalky deposit on the metal, a residue resulting from the metal’s chemical reaction with corrosive elements.
Surface Corrosion’s Impact on Aircraft Metals
- Structural Integrity: The cumulative effect of surface corrosion can pose significant risks to an aircraft’s structural integrity. Over time, the metal can become brittle and more prone to fractures.
- Maintenance Costs: Increased maintenance and repair costs due to the need for regular inspections, treatments, and potential part replacements.
- Aircraft Performance: Corroded surfaces can increase drag and decrease the aerodynamic efficiency of the aircraft.
Surface Corrosion’s Prevention and Treatment
- Regular Inspections: To detect early signs and implement timely maintenance measures.
- Protective Coatings: Application of corrosion-resistant coatings or paints.
- Environmental Control: Storing aircraft in controlled environments, like hangars, can reduce exposure to corrosive agents.
Fretting Corrosion
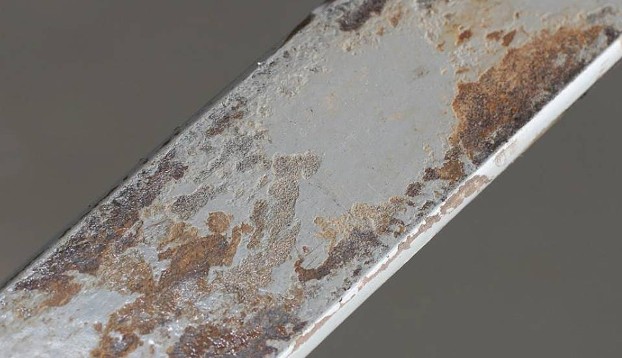
Fretting corrosion arises within an aircraft from repeated wearing, rubbing, or vibration of two materials against each other in a corrosive medium.
Fretting Corrosion’s Appearance on an Aircraft
The result is a roughened, often oxidized surface at the contact points, which can weaken the material’s integrity.
Fretting Corrosion’s Impact on Aircraft Metals
Components in close contact and subject to vibration or movement, such as fasteners, bearings, or overlapping surfaces, are particularly susceptible to this type of aircraft corrosion. The fine wear debris can act as an abrasive, exacerbating material loss.
Fretting Corrosion’s Prevention and Treatment
Proper lubrication, alignment, and securing of components are essential to preventing fretting corrosion within an aircraft. Using materials that resist fretting or applying protective coatings can also help reduce the risk. Regular maintenance checks can identify areas of concern, allowing for adjustments or replacements as needed.
Dissimilar Metal Corrosion
Dissimilar metal corrosion, which is also known as galvanic corrosion, arises when two different metals or alloys come into direct contact with one another and are joined by an electrolyte, typically moisture. This electrochemical process is driven by the potential difference between the metals in the galvanic series.
Dissimilar Metal Corrosion’s Appearance on an Aircraft
The corroding metal (anode) will show signs of degradation, while the protected metal (cathode) remains unaffected. The corrosion often appears more aggressive at the junction where the two metals meet.
Dissimilar Metal Corrosion’s Impact on Aircraft Metals
- Material Degradation: One of the metals, typically the more anodic one, will corrode preferentially, leading to material loss.
- Component Failure: Over time, the corroded component can weaken, leading to potential failures in critical systems.
- Increased Maintenance: Components affected by galvanic corrosion may require more frequent replacements or repairs.
Dissimilar Metal Corrosion’s Prevention and Treatment
- Insulating Barriers: Using barriers or coatings between different metals to prevent direct contact.
- Material Selection: Being aware of potential galvanic couples when selecting materials for aircraft components.
- Regular Inspections: To detect early signs and implement timely maintenance measures.
Intergranular Corrosion
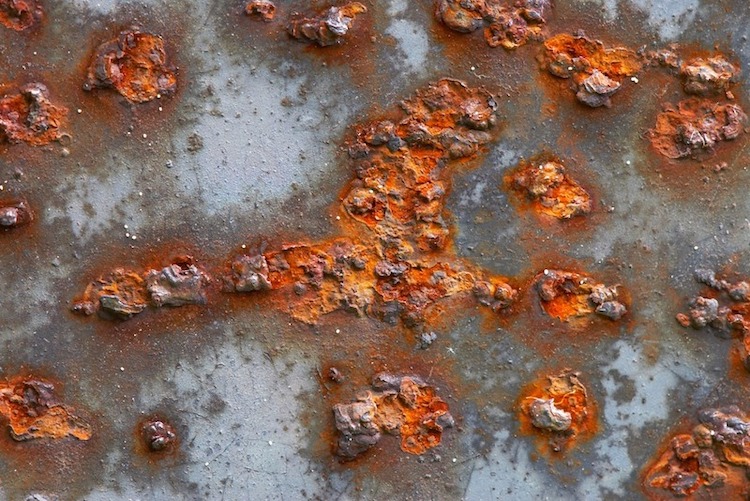
Intergranular corrosion targets the grain boundaries of a metal or alloy. While the grains themselves might remain unaffected, the boundaries possess different electrochemical properties than the grains, causing them to become the primary sites of attack.
Intergranular Corrosion’s Appearance on an Aircraft
The insidious element of this corrosion type is that the metal may appear unblemished on the surface, but microscopic examination can reveal corrosion along the grain boundaries. In advanced stages, the metal can exhibit flaking or separation along these boundaries.
Intergranular Corrosion’s Impact on Aircraft Metals
- Structural Weakness: The metal can be severely weakened internally, even with minimal surface degradation.
- Hidden Dangers: Components might look structurally sound on the outside but could be compromised internally.
- Component Failure: The weakened metal can lead to potential failures in critical aircraft systems.
Intergranular Corrosion’s Prevention and Treatment
- Proper Heat Treatment: Ensuring metals undergo appropriate heat treatments to reduce susceptibility.
- Material Selection: Using alloys known to resist intergranular corrosion.
- Advanced Inspections: Employing techniques that can detect subsurface defects, ensuring early detection and intervention.
Stress-Corrosion Cracking (SCC)
SCC results from the combined action of tensile stress and a corrosive environment on susceptible materials. Unlike other corrosion types, the primary concern here is the initiation and propagation of cracks.
SCC’s Appearance on an Aircraft
Stress corrosion cracking may first manifest itself in fine ruptures that can be challenging to detect in the early stages. However, their thin appearance does not mean that they don’t penetrate deeply.
SCC’s Impact on Aircraft Metals
Certain aluminum and titanium alloys can be susceptible when exposed to specific corrosive agents. The corrosion typically starts at localized stress points, like around fasteners or sharp corners.
SCC’s Prevention and Treatment
Maintenance often involves non-destructive testing methods to identify potential SCC sites. Proper material selection, protective coatings, and stress-relief treatments are crucial for risk reduction. Avoiding designs that introduce unnecessary tensile stresses can also help.
Galvanic Corrosion
Also known as bimetallic corrosion, galvanic corrosion occurs when two different metals or alloys come into direct contact in the very presence of an electrolyte, typically moisture.
Galvanic Corrosion’s Appearance on an Aircraft
The corroding metal (anode) will show signs of degradation, while the protected metal (cathode) remains unaffected. Corrosion is often more aggressive at the junction of the two metals.
Galvanic Corrosion’s Impact on Aircraft Metals
In environments with prevalent moisture, the risk of galvanic corrosion increases, especially if salts or other contaminants are present. For this reason, planes frequently positioned near oceans may be at a higher risk for this type of corrosion.
Galvanic Corrosion’s Prevention and Treatment
Given the variety of metals and alloys in aircraft construction, it’s essential to use insulating barriers, sealants, or coatings to prevent direct metal-to-metal contact. Regular inspections and cleaning to remove salts or contaminants can also help mitigate risks.
Crevice Corrosion
Crevice corrosion is localized and occurs in confined spaces or crevices where the environment can become more corrosive than the surrounding area.
Crevice Corrosion’s Appearance on an Aircraft
The confined spaces can trap stagnant liquid, leading to a change in local chemistry. As oxygen is consumed, a differential aeration cell is created, causing the inside of the crevice to corrode.
Crevice Corrosion’s Impact on Aircraft Metals
In aircraft, areas like joints, seams, fastener heads, or under gaskets and seals can become sites for crevice corrosion.
Crevice Corrosion’s Prevention and Treatment
To prevent it, designs should minimize tight spaces where moisture can be trapped. Using sealants or coatings should be used to protect vulnerable areas. Regular inspections are very crucial for early detection and intervention. Ensuring proper drainage and ventilation can also help in preventing moisture accumulation.
Risk Factors That Increase the Likelihood of Corrosion Within an Aircraft
The overall frequency and quality of maintenance play a large role in preventing the onset or accumulation of corrosion within an aircraft. However, there are additional risk factors worth highlighting, including:
- How the planes are stored – Your choice of hangar can noticeably contribute to the onset of corrosion. The ideal choice would be to use a heated hangar, though insulated alternatives also provide a degree of protection. Remember, the more protection from the elements, the better!
- Where the airplane primarily operated – An aircraft that spent significant time in regions with high humidity are more likely to develop multiple types of corrosion.
- Certain models are particularly prone to specific types of corrosion – For example, operators of select Cessna models from the 1980s report an above-average occurrence of filiform corrosion. Our recommendation is to thoroughly research any specific corrosion risks associated with the type of aircraft you operate by consulting with reputable online forums or through in-person networking.
Key Takeaways About Corrosion Prevention and Identification in an Aircraft
The integrity and safety of plane parts are paramount, making understanding and preventing types of aircraft corrosion an essential aspect of maintenance and design. As we’ve explored, corrosion can manifest in various forms, from the surface-level degradation seen on aluminum surfaces to the more complex alloy structure breakdowns.
Recognizing the early signs of these types of corrosion and understanding the corrosion-producing agents present are the first steps in prevention. Equally important are the maintenance practices employed to counteract these corrosive forces.
The best way to avoid the onset of corrosion is to use aircraft corrosion inhibitors, regular inspections, and proper coatings; avoid galvanic couples; and ensure appropriate heat treatments. In turn, you can significantly extend the life of aircraft components and ensure the safety of those onboard.
For additional reading to assist with essential airplane part maintenance with increased accuracy and efficiency, check out:
- Types of Aircraft Checks – Line, Base, and MRO
- AI in Aviation: The Future of Buying & Selling Parts
- Aerospace Supply Chain Challenges and Potential Solutions – 2024 Predictions
- Aircraft Parts Inventory Management & 8 Mistakes to Avoid
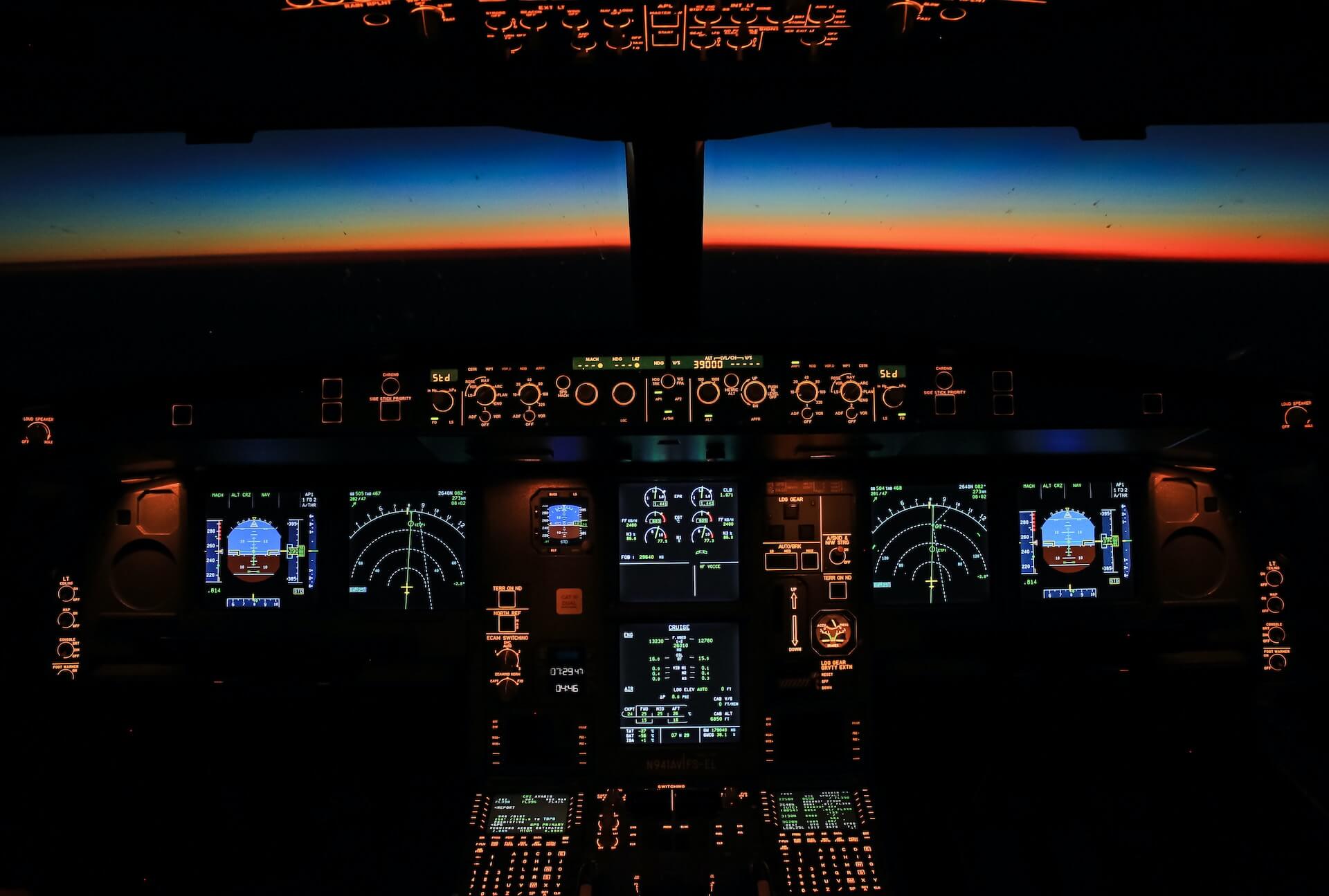
Written by Michael Olusoji
Michael Olusoji is a distinguished aviation writer with over five years of in-depth expertise.
His comprehensive research and analytical prowess have culminated in a myriad of articles that dissect the intricate facets of the aviation sector, particularly the engineering nuances of aircraft components.